B737-500 Throttle Conversion to NG Style - Overview
/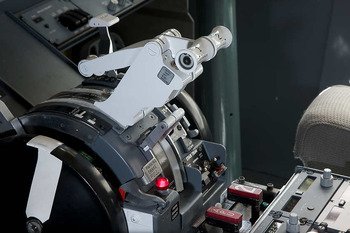
This is the second throttle unit I’ve owned and based on experience, there are many changes that have been implemented that are different to the earlier unit.
The throttle quadrant is a relatively complicated piece of kit. To do it justice, rather than write about everything in one very long post, I’ve decided to divide the posts into sections.
This is the first post that will deal with the general attributes of the throttle unit, interface cards used and touch on the automation and motorization of the unit. Further detailed posts will address individual functionality, conversion and troubleshooting.
Historical Perspective and Conversion
The throttle quadrant and center pedestal were removed from an Alaskan Air Boeing 737-500 airframe. I purchased the unit directly from the teardown yard in Arizona (via a finder).
The conversion to full automation and motorization was not done by myself, but by a good friend of mine who is well versed in the intricacies of the B737 and in the various methods used to install automation to a throttle unit. I am very fortunate to be friends with this individual as in addition to being an excellent craftsman with a though understanding of electronics; he is also a retired Boeing 737 Training Captain.
forward bulkhead of oem 737-500 throttle
New Design
The new throttle unit has been converted to Flight Simulator use based on a new design. The interface cards, rather than being mounted on the forward bulkhead have been mounted within the Interface Master Module (IMM) which is separate to the actual throttle unit. The DC motors required for throttle and speed brake motorization are mounted forward of the throttle unit (in the traditional location).
Connection from the throttle to the IMM is via specially-adapted VGA cables and D-Sub plugs. This keeps the unit clean of unsightly wiring and interface cards. it also keeps loose cables and wires to a bare minimum on the outside of, and inside the unit; automation and motorization means that there are now moving parts and it’s important to separate delicate cards and wiring away from mechanically moving parts
This is in stark contrast to my first throttle that had the interface cards mounted directly on the forward bulkhead and within the unit.
In addition, micro buttons have been used in some circumstances to counter the traditional method of using potentiometers to control calibration of the speed brake, flaps and throttles.
Components - Interface Cards and Motors
Conversion of any OEM part to operate within Flight Simulator requires interface cards. The following cards are used to convert analogue outputs to digital inputs for the throttle unit. The cards also provide functionality for the fire panel, landing gear, yaw dampener, flaps and brake pressure gauges on the Main Instrument Panel (MIP). All cards are mounted on the separate Interface Master Module (IMM).
Alpha Quadrant Motor Controller card A - TQ automation & logic CMD A channel
Alpha Quadrant Motor Controller card B - TQ automation & logic CMD B channel
Phidget High Current AC Motor Controller card – Provides two channels for trim wheel speeds and trim wheel movement
Phidget Motor Controller Advanced Servo card – Provides the interface or bridging between the Alpha Quadrant cards and flight avionics and CMD A
Phidget Motor Controller Advanced Servo card - Provides the interface or bridging between the Alpha Quadrant cards and flight avionics and CMD B
Phidget Motor Controller Advanced Servo card – Movement of flaps gauge
Phidget Motor Controller Advanced Servo card – Movement of trim tab indicators
Leo Bodnar BU0836 A Joystick Controller card – Controls all switches & buttons on TQ
PoKeys 55 card - Flaps (buttons)
Phidget 0/0/8 relay card – Speed brake, auto throttle relays CMD B, fire panels, trim wheel revolution speed on CMD B
Belkin 7 input USB 6.5 amp powered mini hub (2) – TQ
2 two-stage DC pump motors - Powers the movement of the trim wheels, trim tab indicators
2 electric motor - powers the movement of the speedbrake lever and thrust levers
Phidget Cards
Phidgets cards provide the necessary interface between the throttle and flight simulator. I believe that Phidget cards are probably one of the more reliable cards on the market that can be used to directly interface OEM parts to flight simulator.
In addition to the two Alpha Quadrant cards mentioned above, a Phidget High Current AC Controller card acts as a ‘bridge’ to allow communication between the Alpha Quadrant cards and the avionics suite (in this case ProSim737). This card also provides the connectivity to allow the trim wheels to spin when CMD A or B is selected on the Main Control Panel (MCP).
Trim Tab Indicators and Throttle Buttons
To control the movement of the two trim tab indicators, a Phidget Motor Controller Advanced Servo card is used to control the output to two, two-stage DC motors. These motors, which are normally used to power water pumps, control the variable speed of the trim indicators and the revolution of the trim wheels. The speed which the indicator moves is reliant on the user setting within the “trim section” in the configuration page of the flight avionics software.
A Leo Bodnar BU0836A Joystick Controller card is used to control all switches and buttons on the throttle unit, while a Phidget 0/0/8 relay card is used to turn logic on and off that controls the actions of the speed brake.
white colour of next generation thrust levers is unmistakable
Automation
Essentially, automation is the use of CMD A or CMD B (auto pilot) to control the N1 outputs of the throttle, and motorization is the moving of the throttle levers in unison with N1 output.
Automation is achieved by the use of two main motor controller cards (Alpha Quadrant cards); one for CMD A and another card for CMD B. Each card operates separately to each other and is dependent upon whether you have CMD A or CMD B selected on the Main Control Panel (MCP).
The Alpha Quadrant cards provide the logic from which the automation of the throttle unit operates.
Being able to program each card allows replication of real aircraft logic and systems. Whenever possible, these systems and their logic have been faithfully reproduced..
Main Controller Cards (thanks NASA)
The controller card I have used is not a Phidget card but a specialist card often used in robotics (Alpha Quadrant card). The software to program the card has been independently developed by a software engineer and does not utilize Phidgets.
The technology used in the controller card is very similar to that utilized by NASA to control their robotic landers used in the space industry. The technology is also used to control robots used in the car industry and in other mass production streams. One of the benefits of the card is that it utilizes a software chip that can be easily replaced, upgraded or changed.
cp flight mcp
CMD A/B Auto Pilot - Two Independent Systems
Most throttle units only use one motor controller card which controls either CMD A or CMD B; whichever auto pilot you select is controlled by the same card.
In the real aircraft to provide for redundancy, each auto pilot system is separate. This redundancy has been duplicated by using two Alpha Quadrant controller cards, rather than a single card. Each controller card has been independently programmed and wired to operate on a separate system. Therefore, although only one CMD is operational at any one time, a completely separate second system is available if CMD is selected.
Synchronized or Independent Motorization
Synchronization refers to whether the two throttle thrust levers, based upon separate engine N1 outputs, move in unison with each other (together) or move independently.
In the real aircraft, on earlier airframes, the levers were synchronized; however, the NG has a computer-operated fuel control system which can minutely adjust the N1 of each engine. This fuel management can be observed in a real aircraft whereby each throttle lever creeps forward or aft independent of the other lever.
Programming flight simulator to read separate N1 outputs for each engine and then extrapolating the data to allow two motors to move the throttle levers independently is possible; however, the outputs are often inaccurate. This inaccuracy can be seen on reproduction throttle units that show huge gap between lever one and lever two when automating N1 outputs.
I decided to maintain the older system and have both levers synchronized. If at some stage in the future I wish to change this, then it’s a matter of adding another motor to the front of the throttle bulkhead to power the second thrust lever.
Although the TQ is automated, manual override (moving the thrust levers by hand) is possible at any time as long as the override is within the constraints of the real aircraft logic and that provided by the flight avionics (ProSim737).
electric motors provide the power to move the thrust levers and speedbrake lever
Motors
Four motors are used in the throttle unit.
Two electric motors are mounted forward of the bulkhead. These motors power the movement of the throttle levers and speed brake. Two DC pump motors are installed directly within the throttle unit and power the movement of the trim wheels and trim tab indicators.
A clutch system is also mounted to a solidly mounted frame on the forward bulkhead. The clutch system is used by the speed brake. The method of locomotion between clutch and thrust levers is a standard automobile style fan belt.
To allow both thrust levers to move in unison, a bar linking the lever which is motorized to the non-motorized lever was fabricated and attached to the main shaft of the motor.
The motors chosen were automobile electric window motors. These motors are powerful, provide excellent torque and were selected due to their reliability and ease of use.
flight simulator using oem throttle
Trim Wheel Spinning
The trim wheels can spin at two different speeds dependent upon whether the auto pilot is engaged or whether automation is turned off (manual flying). A Phidget High Current AC Controller card is used to interface the spinning of the trim wheels. The Phidget card has two channels and each channel can be programmed to a different revolution speed. The speed of the revolutions is controlled directly within the Phidget Advanced menu within the ProSim737 software.
The system was duplicated using a second Phidget card to ensure that both CMD A and CMD B operated identically.
In the real aircraft there are four different revolution speeds dependent upon the level of automation and the radio altitude above the ground. Although it is possible to program this logic into the Alpha Quadrant cards and bypass ProSim737 software, it was decided not to as the difference in two of the four speeds is marginal and probably unnoticeable. Further, the level of complexity increases somewhat programming four speeds.
Trim Wheel Braking
In the real aircraft, the trim wheels have an effective braking mechanism that stops the trim wheels from spinning down; basically it’s a brake. Testing of a military specification motor with brakes to stop wheel movement was done; however, the motors were too powerful and whilst the trim wheels did stop spinning, the noise and jolt of the brake activating was not acceptable.
Functionality and Configuration
The TQ has been converted to allow full functionality, meaning all functions operate as they do in the real Boeing aircraft. Speed brake, flaps, parking break, reverser levers, thrust levers, trim stabilizer runaway toggles, trim tab indications, TOGA and A/T buttons, horn cut out, fuel levers and two speed trim wheel spinning have been implemented.
These functions and the process of conversion and calibration (potentiometers and micro buttons) will be addressed in separate posts.
Configuration, if not directly to the Alpha Quadrant cards via an external software program is either directly through the avionics suite (ProSim737) and the Phidgets card software or through FSUIPC. Where possible, direct calibration and assignments via FSX have not been used.
oem 737-500 backlighting
Backlighting
The throttle unit's light plates, with the exception of the parking brake which is illuminated by a 28 Volt bulb, are back lit by 5 Volt aircraft bulbs. A dedicated S150 5 Volt 30 amp power supply is used to supply power to the bulbs.
Stab Trim T-Locker Toggles
The only function which is different from the real aircraft is the stab trim switch. The left hand toggle operates correctly for runaway trim; however, the right hand toggle has been configured that, if toggled to the down position, the trim wheels will stop spinning. The toggle is a basic on/off circuit and stops current going to the motors that move the trim wheels.
The reason for doing this is that I often fly at night and spinning trim wheels can be quite loud and annoying to non-flyers… The toggle provides a simple and easy way to turn them on or off at the flick of a switch.
oem 737-500 t-lockesr
Finding T-Lockers
Finding T-Locker toggles that are used in the NG series airframes is not easy. Reproduction units are available but they appear cheesy and rarely operate effectively as an OEM toggle. Earlier airframes used metal paddles (my earlier 300 series throttle used these type of trim switches) while the 400 series uses a different style again. Trim switches are usually removed and reinstalled into an aircraft; therefore, I was fortunate that the throttle unit I secured had the later model T-Lockers.
The switches are called T-Lockers as you must manually pull down the cover from each switch before pulling the toggle downwards. This is a safety feature to ensure that the toggles are not inadvertently pushed by the flight crew.
Thrust Handles - Colour
The colour of the throttle quadrant between the 737 aircraft variants leading towards the Next Generation series is similar, however, the colours are slightly different on the Next Generation throttle are different.
First, the thrust levers are not painted, but are cast in the actual colour. Despite this, older aircraft will exhibit UV fading causing the thrust levers to appear darker and yellower.
There is no distinct RAL colour, however, RAL 7047 is very close. The colour of the thrust levers is identical to the side walls, knobs and liners. The bac hex colour designation in BAC#705 (Federal STD 595B-36440). If you do not understand the various colour definition, search google for further information.
Importantly, it is almost impossible to find the correct colour codes as Boeing guards this information carefully to ensure it is not copied by rival aircraft manufacturers (why I am not sure).
Center Pedestal - Cabling and Wiring
The three-bay center pedestal, mounted directly behind the throttle unit, has a number of cables and connections required for individual panel operation. Rather than have these cables weave through the mechanism of the throttle (remember this is an automated throttle and there is considerable movement inside the unit), I’ve opened a hole into the platform directly under the pedestal.
Any wiring or cabling is routed through this hole into a piece of round flexible conduit tubing (it’s actually the hose from a disused washing machine). The cables, after making their way to the front of the platform, then connect either to the computer or the Interface Master Module.
The use of flexible tubing is not to be underestimated as any cabling must be protected to avoid the chance of snagging on the under-floor yoke and rudder mechanisms which are continually moving.
More Pictures (less words...)
To see further pictures, navigate to the Image Gallery.
In this post we have discussed a general overview of the throttle quadrant and examined the automation and motorization. We also have looked at the interface cards used and studied the stab trim T-Lockers in more detail. In future posts we will examine the different parts of the throttle unit and learn how they were converted and calibrated to operate with Flight Simulator.
Click any mage to make it larger.
UPDATED 16 August 2022